Eisenherstellung im Rennofenverfahren
Das Rennfeuerverfahren / Rennherd und Rennofen /Skizzen / Bilder: Rennherd bei Nacht
Eisen wurde in sogenannten keltischen Hochöfen gewonnen.
Dies waren, einfach gesagt, meist kegelförmige 0,6 bis 1,50 Meter hohe, aus Lehm und Flechtwerk gemauerte schornsteinartige Röhren, mit einer Ofengrube im Boden. Diese Öfen wurden nach dem Benutzen umgestoßen, damit man an das Eisen gelangen konnte. Dadurch sind heutzutage kaum noch Spuren von ihnen zu finden.
Schon die Römer verwendeten solche Öfen.
Das die-roemer-online.de - Team war Teilnehmer am 2. Internationalem Rennofensymposium in Polle und Initator des 1. und 2. Rheinischen Rennfeuertreffens!
Grundsätzliches zum Rennfeuerverfahren
Die mineralogischen Untersuchungen an Schlackeresten ergaben, dass die Römer
ihr Eisen in Rennfeueröfen oder Rennherden erzeugten. Der Rennfeuerprozeß
ist eine Technik, die seit der Entwicklung der Hochöfen im Spätem
Mittelalter in Europa allmählich in Vergessenheit geriet.
Im Hochofen erreicht man sehr hohe Temperaturen, bei denen das metallische
Eisen in den flüssigen Zustand übergeht und infolge von Kohlenstoffaufnahme
zu Gußeisen wird, das erst nach einem Frischungsprozess (Abkohlung)
schmiedbar ist. Im Rennfeuer hingegen erfolgt keine Schmelzung des Eisens,
(es wir nur sehr weich, wie zäher Teig) da die Temperaturen nur bei etwa
1200 - 1300°C liegen, dafür ist das Eisen nach einer erfolgreichen Verhüttung aber sofort schmiedbar.
Doch das metallische, schwammartige Endprodukt ist noch verunreinigt durch
Schlacke und Holzkohlenreste und kann erst nach dem Prozeß des Faltens und
Hämmerns zu reinem Eisen umgearbeitet werden
"reines" Eisen oder gar Stahl waren (im Vergleich zu heute) kostbare Rohstoffe;wenn auch viel billiger als Kupfer oder Bronze.
Mehr zur Geschichte des Eisens finden Sie hier.
Brennmaterial:
Es wird fast ausschließlich Holzkohle verwendet , je nach Ofengröße 30 bis über 200 kg und auf etwa 2 bis 5 cm Größe zerstoßen.
Wir sollten uns hier auf etwa 20 bis 30 Kilo einrichten.
Holzkohle wird in einem langwierigen Prozess durch "Backen"(Verkohlen) von
Holz (bevorzugt Buchenholz )in Kohlemeilern gewonnen (etwa 300°C).
Erz:
"Harte Erze" wie Hämatit, Magnetit, Limonit, "weiche" wie diverse Sumpf- oder Raseneisenerze,
zu kleinen Bröckchen bis Sandstärke (Eisengehalt des Erzes mind. 50 %, ist der Eisengehalt zu gering, entsteht kein/kaum Eisen, da nur 50 % überhaupt gewonnen werden).
Früher wurde auch Eisen- oder Stahlschrott, bzw. unbrauchbare Luppen in den Ofen zurück gegeben. Es kann auch Rost und der beim Schmieden anfallende Hammerschlag verwendet werden, jedoch sollte hier Erde oder Kehricht als Schlackenbildner zugesetzt sein.
Jedes Erz braucht unterschiedliche Temperaturen bzw. Luftmengen
(Faustregel: Je "härter" und gröber das Erz, desto mehr Hitze - also Luft- wird benötigt damit es aufgeschmolzen wird).
Sonstige Materialen:
Großvolumiger Blasebalg (siehe Bauanleitungen),
Edelstahl- oder besser Ton- oder Keramikdüse (zur Herstellung von Tondüsen), Schutzkleidung, Handschuhe,
Spaten, Lehm oder Ton, Reisig und Stroh, Ziegel etc. zum Ofenbau.
Auch ein großer Holzklotz und großer Holzhammer zum Verdichten der Luppe,
eine Luppenzange, eine große Stahlbrechstange und ein starker Weidenstock zum
Reinigen der Düse sind von Vorteil.
Zur Kontrolle des Schmelzvorganges ist ein Blauglas oder eine Schweißerbrille hilfreich.
Exkurs: Warum ein Verdichtungshammer aus Holz?
Man verwendet einen Holz- und keinen normalen Metallhammer,
weil zum einen das Metall einen Großteil der Hitze absorbieren würde,
die Luppe also schnell auskühlt und weniger lang verdichtet werden kann und zum anderen,
weil die glühende Luppe (oder besser Reste davon) unter Umständen am Metallhammer festkleben könnte.
Deshalb sollte man auch Düsen aus Metall mit einem Holzstock und nicht mit einer Metallstange von Schlacke befreien.
Reduzierende Bedingungen:
Die Bildung metallischen Eisens erfolgt unter sauerstofffreier Atmosphäre,
d.h. die Beschickung aus Eisenerz und Holzkohle muss unter Luftabschluss
gehalten werden. Dies wird dadurch erreicht, dass die Öfen schachtartige
oder kuppelförmige Aufbauten aus Strohlehm haben, mit einer Gichtöffnung zum
Beschicken des Ofens während des Prozesses.
Windzufuhr:
Natürlich darf der Luftabschluss nicht total sein, sonst kann die glühende
Holzkohle nicht die erforderliche Temperatur von 1200°C erreichen. Es muss
also eine Luftzufuhr geben, die entweder durch natürlichen Luftzug (Kamineffekt) erfolgt, wofür der Schacht sehr hoch sein muss oder (fortschrittlicher) durch einen größeren Blasebalg - oder mehreren kleinen.
Es darf auch nicht übertrieben viel Luft eingeblasen werden, da das gebildete Eisen sonst wieder verbrennt
(sichtbar z.B. an funkensprühender Schlacke). Der "richtige Wind" muss bei jedem Ofen und Erzsorte individuell erprobt werden, Misserfolge bei den ersten Versuchen sind nicht selten.
Auffangen der Schlacke:
Die Schlacke muss von der Luppe getrennt werden. Entweder sie sammelt sich
in einer besonders tiefen Ofengrube (Ofensumpf) zwischen Reisig und Astwerk oder sie muss während des
Prozesses abgelassen werden. Die Schlacke ist ein wichtiger Indikator für den Prozess.
Eine orange-gelb glühende wie Dickmilch rinnende, nicht funkensprühende Schlacke ist meist ein gutes Zeichen für
ideale Reaktionsbedingungen.
Prozessdauer: Etwa 5 bis 9 Stunden, je nach Material, Lust und Laune.
Rennherd und Rennofen
In der römischen Antike waren unterschiedliche Ofenformen in Gebrauch, wobei die Rennherde als die urtümlichste Form aufgefasst werden. Dieser Typus war relativ einfach zu errichten, verbrauchte aber auch mehr Kohle und ergab weniger Eisen als seine moderneren, bzw. mittelalterlichen Vertreter.
Bei der Eisenverhüttung wurden in allen Zeiten enorme Mengen an Brennstoff verbraucht: etliche Kilo Holz zum Vorheizen des Ofens, bis zu 10 Kilo Kohle ( die erst mal aus noch mehr Holz produziert werden musste) zum weiteren Einheizen und sicher weitere 20 bis 40 Kilogramm Kohle für Erz, aus dem dann vielleicht 3 bis 5 Kilo Eisen werden, wenn man Glück hat, das Ausschmieden nicht mitgerechnet.
Größere Öfen brauchten natürlich noch viel größere Mengen.
Wir wollen hier die Verhüttung in einem kleinen Rennherd und in einem etwas größeren Rennofen beschreiben. Der Rennherd ist mehr oder weniger wiederverwendbar, die Schlacke kann abgestochen werden. Der Rennofen ist eine "Einmalkonstruktion".
Skizzen
Rennherd bei Nacht
Hier einige außergewöhnliche Bilder von unserem Rennherd,
aufgenommen beim 2. Internationalen Rennofensymposium in Polle 2005.
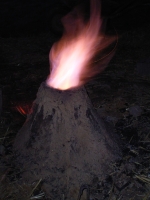 |
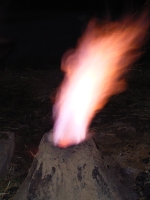 |
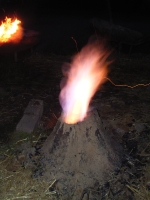 |
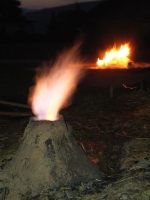 |
Rennherd bei Nacht |
Rennherd bei Nacht |
Rennherd bei Nacht |
Rennherd bei Nacht |
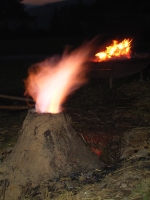 |
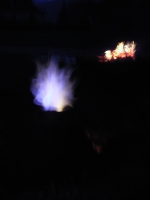 |
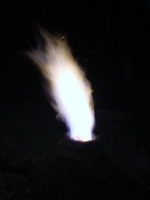 |
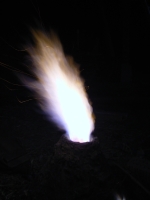 |
Rennherd bei Nacht |
Rennherd bei Nacht |
Rennherd bei Nacht |
Rennherd bei Nacht |
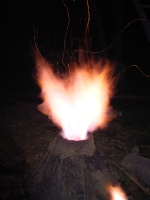 |
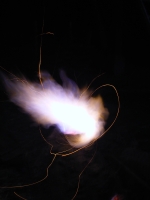 |
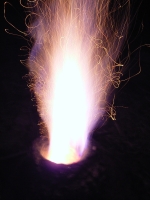 |
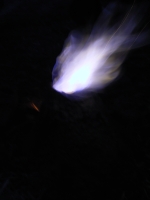 |
Rennherd bei Nacht |
Rennherd bei Nacht |
Rennherd bei Nacht |
Rennherd bei Nacht |
Informationen zum die-roemer-online.de - Rennherd finden Sie hier.
Links:
Geschichte der Eisenherstellung
Der die-roemer-online - Rennherd
Verschiedene Rennofentypen - Ein Vergleich
Damast & Stahlherstellung
Rennherdversuch 8.-10.09.2008
Rennfeuertreffen Luxemburg 15.-16.05.2008
2. Rheinisches Rennfeuertreffen 24.-26.08.2007
Bergbautag Imsbach 30.06-01.07.2007
1. Rheinisches Rennfeuertreffen 25.-27.08.2006
Erfolgreicher Rennherdversuch (17.09.2005)
2. Internationales Rennofensymposium 19.-21.08.2005
Rennherdversuch vom 25.06.2005
Projekt: Eisenherstellung
Herstellung eines röm. Messers
Damastmesser zum Selberschmieden
Anleitung: Beilklinge mit Schneidleiste
Zubehör: Tondüsen selbst brennen
Zubehör: 2-Kammerblasebalg
Zubehör: Großer Spitzblasebalg
Die Feldschmiede